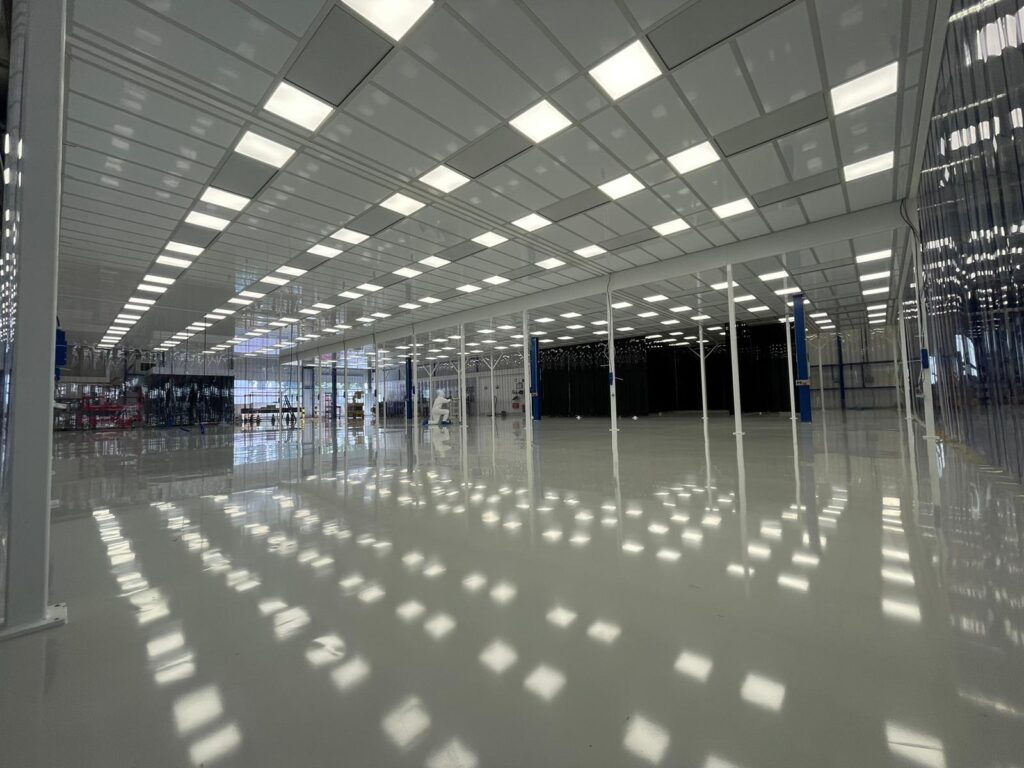
At the premises of VDL-ETG in Almelo our engineers succefully completed the construction of yet another modular softwall cleanroom. The floor area of this large cleanroom is more than 675m² and is connected by means of a corridor to the already existing cleanrooms. The entire project, consisting of Phase x1, x2, x3, now covers almost 1700m² of floor space, completely made up of modular softwall cleanroom. More detailed information about phase x1 and x2 in the case study.