- ISO class 5, 6, 7 (ISO 14644-part 1).
- 9 no. H14 type HEPA fan filter units equipped with high capacity prefilters.
- Dimensions: ca. 115 m², 2.7m int. height.
- Fully flush walls and ceiling with high performance insulation properties (sound and thermal).
- Integrated flush LED panels for optimal lighting according to a predetermined lighting plan.
- Self closing swing doors with interlock system.
- Fully furnished by our accessories and consumables department.
- Dedicated ISO Class 5, UV inspection area.
- Goods transit area to support good practice procedures with feed-through cabinets.
- High capacity air conditioning system for heating and cooling.
The PanelBloc cleanroom
This PanelBloc cleanroom has also been completely engineered and built according to the wishes and requirements of our customer. In this case Roosen Mechatronics, part of Roosen Industries in Eersel. A company founded in 1972 with a rich history and experience in the field of machining, sheet metal works and mechatronics. With more than 250 employees, at 4 different locations in Europe and Asia and now a advanced PanelBloc cleanroom, Roosen Industries has all the competencies in-house to guarantee a very high quality of work.
(ASML) Grade 4 and 2
By installing advanced fan filter units equipped with HEPA H14 main filters and high capacity prefilters, the cleanroom easily achieves an ISO-Class 6 classification in the main and PAL area. In the specially designed UV inspection area, the cleanroom even achieves an ISO-class 5 classification in operations status. This high cleanliness classification makes this cleanroom very suitable for assembling, cleaning and packaging products according to the ASML Grade 4 and 2 standards.
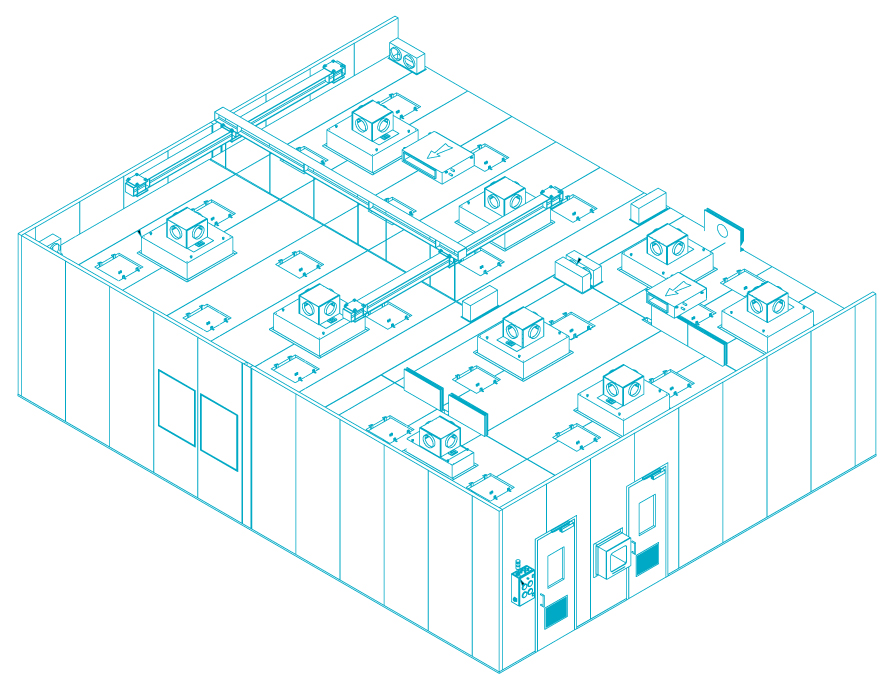
The cleanroom is divided into four different areas (Main, UV inspection, PAL, MAL). The layout and dimensions of the areas are specifically designed for the process that Roosen uses for assembling, cleaning and packaging the products. This allows the cleanroom process to be carried out as efficiently as possible, so that Roossen Mechatronics can guarantee short lead times.
For Roosen Industries, the well-being of the (cleanroom) employees is very important, which is why the cleanroom is equipped with, among other things, a high capacity air conditioning system for heating and cooling, optimal lighting according to a predetermined lighting plan and spacious workplaces are provided. All this to make it as pleasant as possible for the cleanroom employees, which contributes to an efficient work process.
To ensure that the cleanroom can be used optimally in the coming years, consideration has already been given to configuring the workstations differently if this is necessary for different work processes. Additional utilities have already been installed in the main, UV inspection and Mal areas. This makes the cleanroom very flexible for use in different processes, without causing long-term downtime.

The furniture and advice for choosing the right cleanroom products suitable for the work process is fully carried out by the Accessories & Consumables division of ProCleanroom. The specialists of this division, together with Roosen Mechatronics, looked at the wishes and requirements and based this on a package of products such as: stainless steel tables ,cleanroom chairs ,cleanroom cloths, sealing devices, swabs, IPA, clothing and special HEPA cleanroom vacuum cleaners. By running this process in parallel with the construction of the cleanroom, it could immediately be furnished and put into use by Roosen. Rightly to speak of a Full turnkey solution.
- Full turnkey solution – design, hardware, installation, furniture and accessories: a single point of contact.
- Maximum cleanliness performance due to fully flush walls, floor and ceiling.
- Maximum cosmetic appearance for client and supplier presentation.
- Lowest power consumption and operating costs in the market.
Check out our case studies for more completed projects